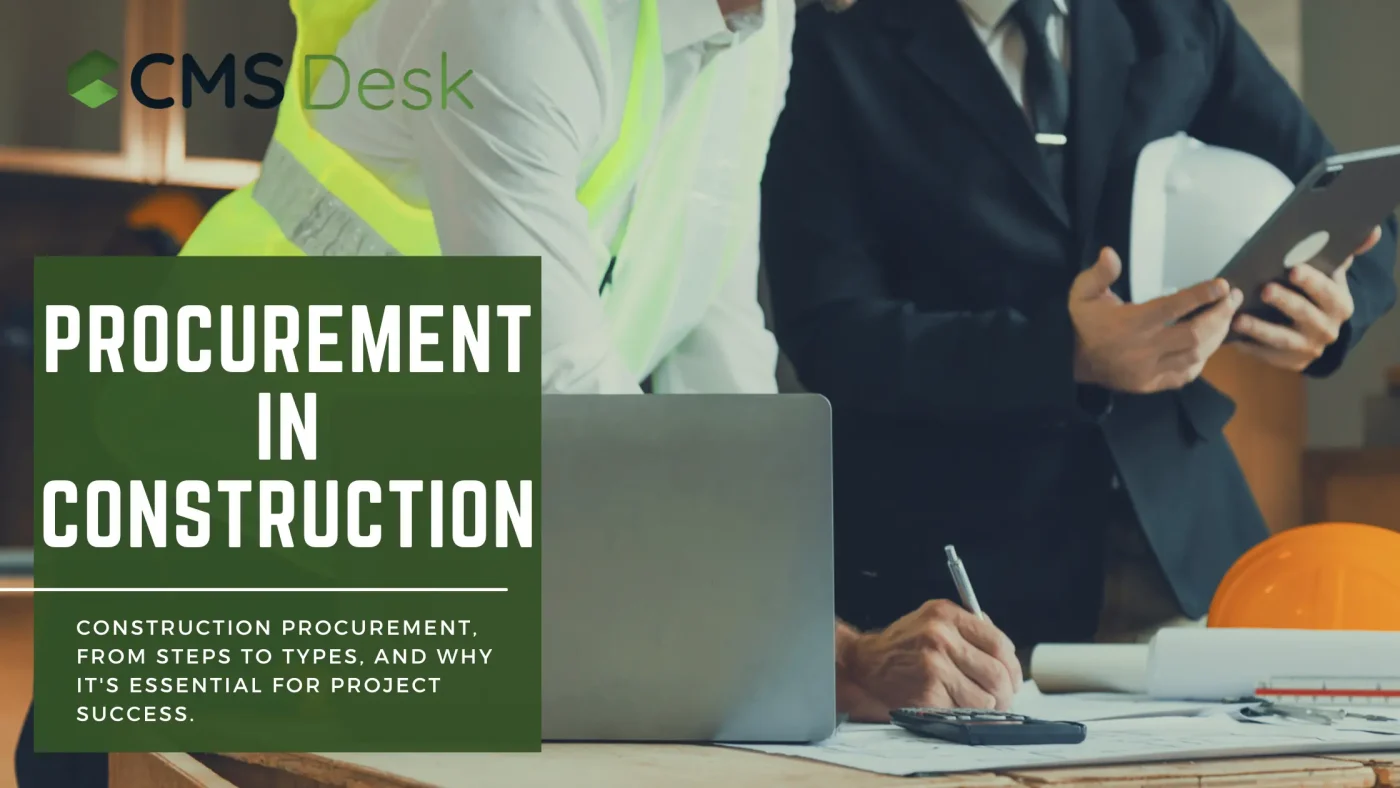
Procurement in construction is about more than just buying materials — it’s the backbone of a successful project, ensuring that the right resources are available at the right time and at the right cost. For beginners, it can feel like navigating a maze of processes and decisions.
This guide will break down what procurement in construction really means, why it matters, the key steps involved, and the different types you’ll encounter. With this clear roadmap, you’ll be better equipped to manage construction projects effectively. And with tools like CMSDesk, streamlining procurement becomes easier, helping you automate tasks, track progress, and make smarter purchasing decisions.
What is Procurement in Construction?
Procurement in construction is a strategic process used to acquire the goods, services, and contracts needed for a project. It ensures that every component, from raw materials to specialised services, is sourced efficiently and cost-effectively.
This isn’t to be confused with simple purchasing, which often focuses solely on transactional exchanges. Procurement involves:
- Planning: Determining project needs and creating procurement schedules.
- Evaluation: Identifying the best suppliers based on quality, cost, and reliability.
- Execution: Managing contracts, purchase orders, and deliveries.
How Procurement Differs from Purchasing
One of the most common beginner questions is about the difference between procurement and purchasing. While these terms are sometimes used interchangeably, they are surely very different:
Procurement is a very complete approach involving planning, negotiation, and supplier relationships. Purchasing is more of a subset of procurement focusing on the actual transaction of placing orders and paying bills. Procurement sets the stage in construction, while purchasing executes the specific tasks.
Why is Procurement Critical in Construction Projects?
The procurement process for construction projects directly impacts timelines, costs, and quality. A poorly managed procurement system can lead to project delays, budget overruns, or compromised safety standards.
Ensuring Timely Delivery
Construction projects operate on tight schedules. Delayed delivery of critical materials, such as steel or concrete, can halt progress and increase labour costs. A robust procurement process minimizes such risks.
Cost Management
Effective procurement helps negotiate better prices and payment terms, reducing overall expenses. Tools like construction procurement software can assist in tracking costs and avoiding overspending.
Maintaining Quality Standards
Choosing reliable suppliers gives you the confidence that materials meet safety and durability standards. This is mainly important for projects in sectors like healthcare or hospitality as the quality directly impacts the user experience.
Steps in the Construction Procurement Process
Understanding the key stages of procurement can simplify the process for beginners. Let’s break it down:
1. Needs Assessment
The first step is identifying what the project requires when we talk about procurement. This involves consulting with architects, engineers, and project managers to list materials, labour, and equipment. For example, a residential building might need flooring materials, plumbing systems, and HVAC units.
2. Market Research
Research the market to understand pricing trends and supplier reputations before approaching suppliers. This lets you get the best value on property and services.
3. Vendor Selection
Finding the right suppliers involves evaluating their reliability, track record, and ability to meet deadlines. Factors you must consider are:
- Past performance on similar projects.
- Pricing and payment terms.
- Certifications or quality standards compliance.
4. Contract Negotiation
Negotiating contracts is a big part in aligning supplier terms with project goals. This step defines deliverables, payment schedules, and penalties for delays. Construction procurement software often comes in handy here and helps in streamlining contract management.
5. Order Management
Once contracts are in place, the next step is issuing purchase orders. This ties closely with purchase order management process as it ensures clear communication about quantities, specifications, and delivery timelines.
6. Delivery and Inspection
Materials are delivered to the construction site, where they are inspected to ensure they meet quality standards. Any discrepancies are reported and resolved promptly.
7. Payment and Closure
The final stage is all about making payments and closing contracts. The procure-to-pay (P2P) process integrates procurement with accounts payable, creating a seamless workflow.
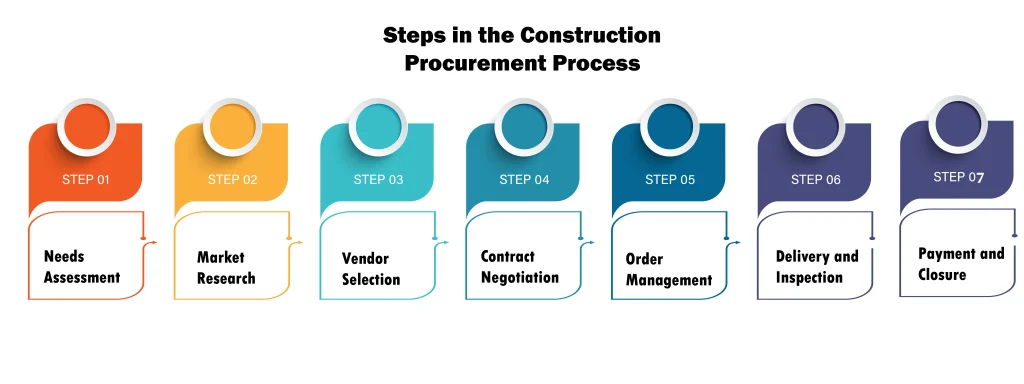
Types of Procurement Methods in Construction
There are a lot of custom approaches to procurement in construction. The method you should choose depends on project size, complexity, and goals.
Traditional procurement is a very straightforward method where the design and construction phases are handled through separate contracts. This approach works best when a detailed design is already prepared, and it allows clear division of responsibilities between designers and builders. However, if changes are required during construction then the separation can sometimes slow down the overall timeline.
1. Design-Build Procurement
It simplifies things by combining both design and construction under a single contract. This method offers better collaboration between the design and construction teams. This then leads to faster project completion. It’s best for projects where speed is crucial and seamless teamwork can help avoid delays or miscommunication.
2. Management Procurement
This approach takes a more hands-on approach by involving a construction manager who coordinates with multiple subcontractors. The manager has to oversee specific activities and handle procurement for various parts of the project. This method is mainly suited for large or very complex projects where multiple workflows need to happen at the same time.
3. Integrated Project Delivery (IPD)
This method focuses on collaboration to bring together all key stakeholders, including owners, designers, and contractors. Everyone shares the risks and rewards. This method works best for innovative or high-stakes projects where close cooperation is essential for success.
Each of these methods has its advantages and challenges. So choosing the right one depends on the specific requirements and goals of your construction project. Understanding these options helps you to align procurement perfectly with your project’s needs.
Challenges in Construction Procurement
Overcoming challenges like supply chain disruptions and vendor reliability often falls under project manager responsibilities, as they work to keep procurement processes on track. The procurement process is a deeply essential one and comes with a lot of hurdles sometimes. One of the most pressing issues people often face is supply chain disruptions. These can be caused by a variety of reasons, including global events, natural disasters, or even logistical failures.
A delay in the delivery of critical materials like steel or concrete that can halt construction progress is a key example of this. The result is increased costs and missed deadlines. Such challenges make it important to maintain flexible timelines.
1. Budget management
Another very common challenge is budget management. Construction projects operate on tight budgets many times. This leaves little room for unexpected expenses. Poor cost estimation platform during the planning phase or sudden fluctuations in material prices can undoubtedly strain project finances.
The rising cost of raw materials like lumber or fuel may require project managers to reassess their budgets and reallocate resources, for example. This causes delays to other aspects of the project.
2. Vendor reliability
This is another area that can complicate procurement. While cost is an important factor in vendor selection, it’s equally crucial to ensure that suppliers can consistently deliver quality materials on time. A single unreliable vendor can disrupt the entire procurement cycle, leading to cascading delays across other project phases.
3. Regulatory compliance
This is also a big concern in construction procurement. Dealing with these regulations can be tough and any oversight may result in penalties, legal disputes, or even project shutdowns. Making sure that all vendors and contractors adhere to local and industry-specific guidelines is a necessary, yet often time-consuming, task.
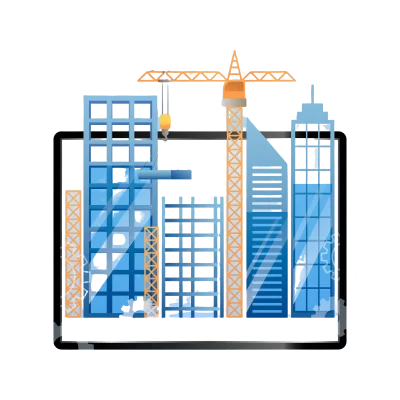
Strategies for Effective Procurement
The most effective strategies we recommend for an effective procurement are:
1. Develop a Comprehensive Procurement Plan
Setting a proactive and strategic approach is is great importance to navigate any procurement challenges. Developing a procurement plan, fostering supplier relationships, and embracing technology.
This plan should outline all key details and include material requirements, delivery schedules, and budget allocations without missing any details. Planning the purchase of materials like concrete and bricks months in advance can help avoid last-minute price hikes and shortages.
2. Foster Strong Supplier Relationships
Building strong relationships with vendors is another very critical strategy that we stand by. Reliable suppliers are without a doubt invaluable assets for your company. They provide quality materials along with giving the flexibility to accommodate changes in project needs.
Having open communication channels, conducting periodic performance reviews, and maintaining mutual trust can surely strengthen these relationships and lead to better long-term partnerships.
3. Embrace Technology
Modern technology has also surely played a very important part in improving procurement efficiency. Construction procurement software is there to automate many time-consuming tasks, such as purchase order management, inventory tracking, and vendor communication.
These tools enable project managers to make informed decisions and streamline the entire procurement cycle by providing real-time updates and reducing manual errors. These software can even send automatic reminders when inventory levels run low. This greatly helps when it comes to timely re-stocking without someone having to constantly check.
4. Prioritise Communication
Having effective HR Platform enhances procurement success even further. Misaligned expectations or unclear instructions can lead to errors, wasted resources, and delays.
Clear communication is for the best of everyone involved. It is to be sure that procurement officers, contractors, or the project managers understand their roles and responsibilities. Regular meetings and updates can keep all stakeholders on the same page and minimize any misunderstandings.
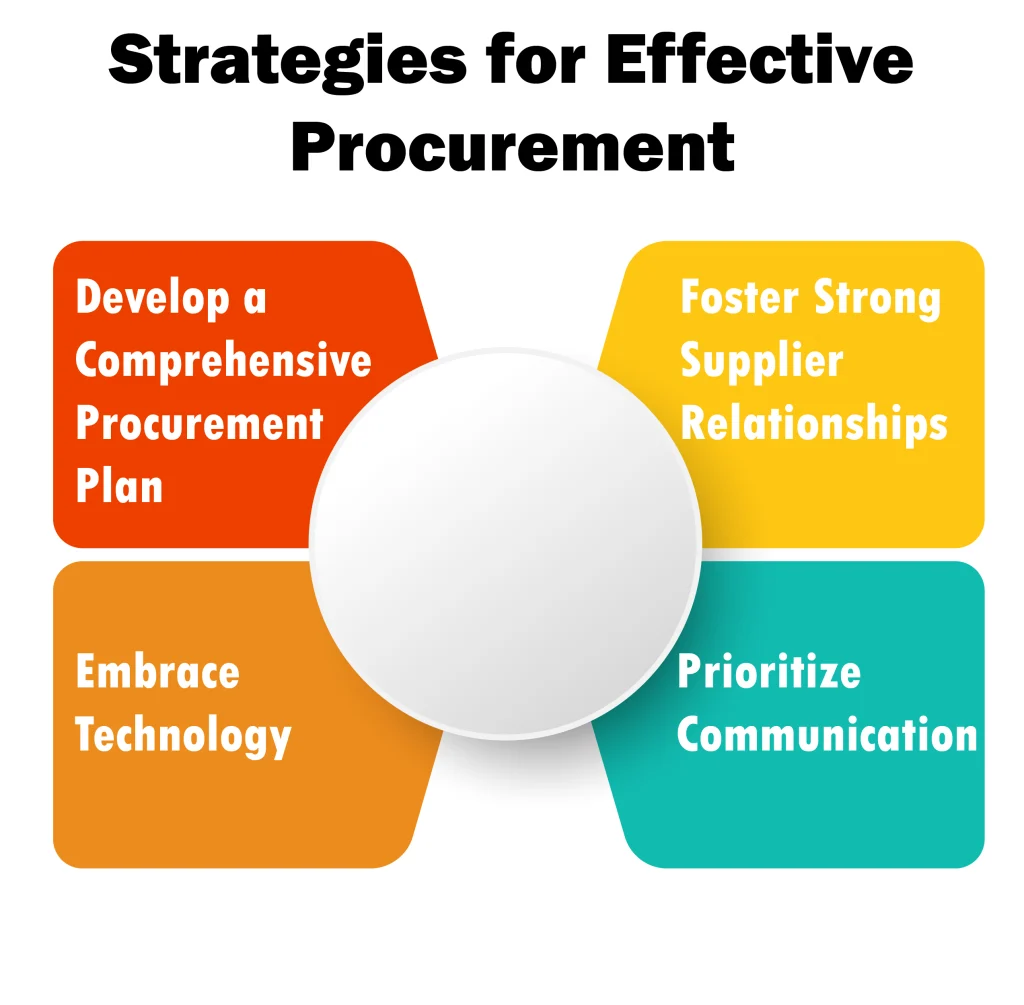
Sustainability in Procurement
Sustainability is now a very critical consideration for managers in construction procurement. This is mostly driven by growing environmental awareness and regulatory requirements.
Companies can actually reduce their environmental impact while appealing to clients who prioritize eco-conscious construction when they decide to adopt sustainable procurement practices.
1. Source Materials Locally
A great way to incorporate sustainability in your procurement is by sourcing materials locally. This will reduce transportation-related emissions while also supporting local economies. We also suggest using recycled or renewable materials as a basic strategy.
Recycled steel and reclaimed wood offer environmentally friendly alternatives where you don’t have to be compromising on quality to save the planet.
2. Focus on Energy-Efficient Procurement
Energy efficiency is also a key focus in sustainable procurement. Investing in energy-efficient equipment and tools can significantly lower energy consumption, reducing both environmental impact and operational costs.
Companies can also implement waste management strategies by collaborating with vendors who have robust recycling programs, ensuring that materials are reused rather than discarded.
Sustainable procurement is more a practical one than just an ethical choice. Governments and industry bodies are trying to bring more strict regulations on carbon emissions and waste management. Including green practices into procurement processes is deeply beneficial for the planet and it is also a smart business move to aim for.
The Role of Technology in Construction Procurement
Technology has undeniably revolutionised procurement in the construction industry. By automating tasks like purchase order creation, inventory tracking, and vendor management, modern tools streamline operations and enhance collaboration. However, with so many tools available, it’s essential to choose the best construction management software to truly maximise efficiency and transparency. Selecting the right solution not only reduces manual effort but also saves valuable time, allowing project managers to focus on critical aspects of construction delivery.
1. Real-Time Data
One of the biggest advantages we take away from technology is real-time data access. The benefits of having procurement software in place are not to be ignored at all. All stakeholders can track material availability and monitor delivery schedules through this software.
It is also really helpful to identify potential bottlenecks from a centralized platform. This level of visibility helps engineers and managers with quicker decision-making. The best part is that it greatly reduces the risk of delays often caused by unforeseen issues.
2. Enhanced Collaboration Between Teams
Technology also improves collaboration between teams greatly. All stakeholders can access the same information by integrating procurement software with other project management tools. This without a doubt helps maintain consistency and reduce any errors.
Contractors can also immediately update procurement officers if material requirements change. This allows adjustments to be made quickly and saves time.
3. Construction Management Software
Even smaller construction companies can benefit from technological advancements. Affordable and user-friendly software options are now available to make it easier for businesses to implement digital solutions. Technology will surely remain a key driver of efficiency and innovation in the industry of construction procurement.
Final Words
Construction procurement is surely a complex process, and as we have discussed, it plays a critical role in the success of any project. It becomes manageable and even rewarding when you put the right strategies and tools to use. A beginner should look to stay informed and focus on fostering strong vendor relationships. Pair this up with embracing innovation and you can streamline procurement processes and ensure better project outcomes.