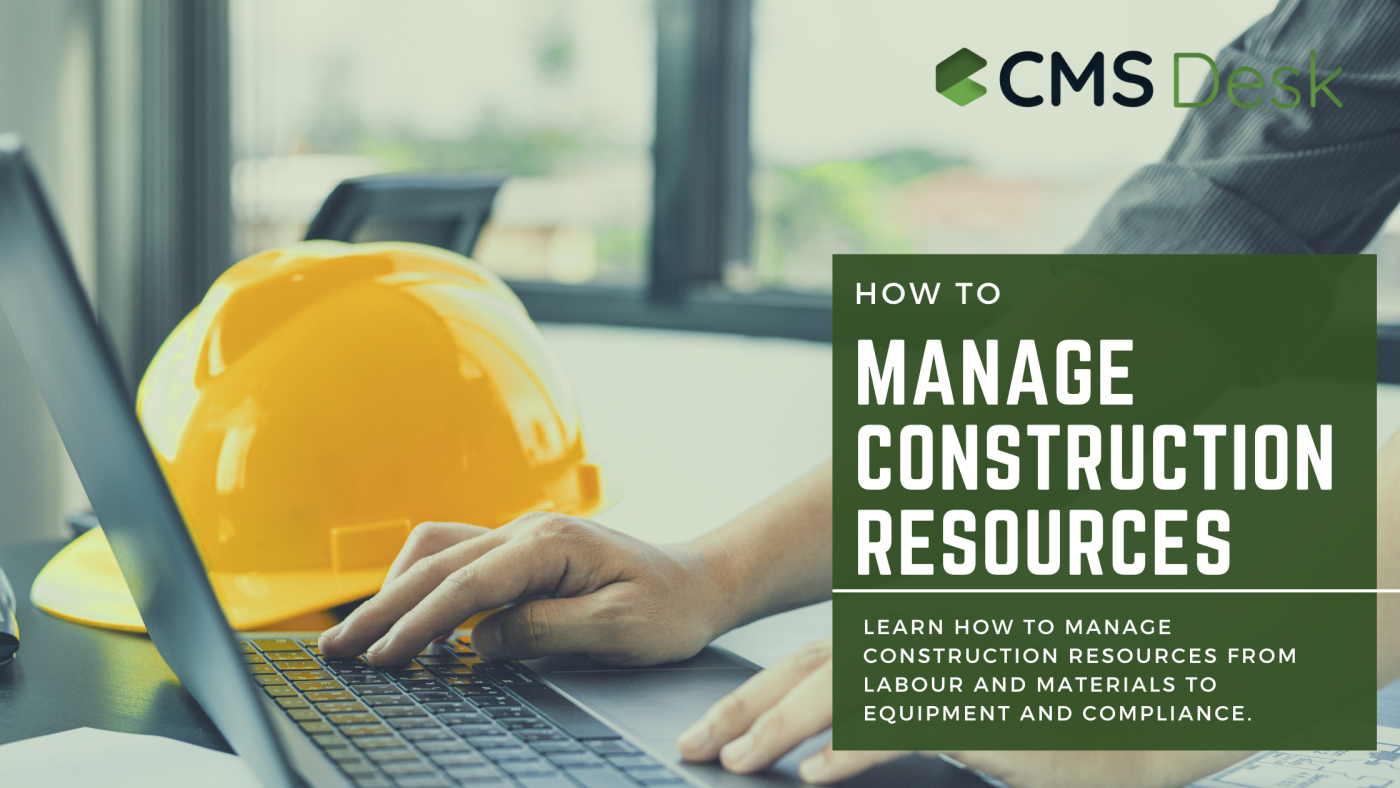
In today’s fast-paced construction industry, the ability to effectively manage construction resources is what separates profitable projects from the ones that miss deadlines, blow budgets, and suffer from constant chaos.
From labour and materials to equipment and time, construction resource management plays a critical role in keeping every project phase on track. When managed well, it improves productivity, cuts costs, and maximises return on investment.
So, how do you master resource management in construction, especially when juggling multiple projects, remote sites, and unpredictable conditions? This guide breaks it all down.
What is Construction Resource Management?
Construction resource management is the strategic process of planning, allocating, scheduling, and monitoring all the critical resources – human, material, and equipment – required to successfully execute a construction project. It plays a pivotal role in ensuring that projects are delivered on time, within budget, and to the expected quality standards.
Effective construction resource management involves the following key components:
1. Labour Management
This includes organising and coordinating the workforce, like engineers, contractors, site supervisors, skilled tradespeople, and general labourers. Proper labour management ensures:
- The right people are assigned to the right tasks based on skill, availability and project phase
- Workforce productivity is optimised to avoid underutilisation or overstaffing
- Labour costs are monitored and kept within planned limits
2. Material Tracking and Procurement
Timely availability of construction materials such as concrete, steel, pipes, bricks, and finishing supplies is critical. A well-managed system enables:
- Accurate tracking of inventory to prevent shortages or overstocking
- On-time procurement aligned with project timelines
- Reduced material waste through better forecasting and site-level control
3. Machinery and Equipment Scheduling
Construction relies heavily on the efficient use of machinery – cranes, excavators, loaders, scaffolding, and more. Managing this resource effectively means:
- Avoiding equipment downtime through preventive maintenance and smart scheduling
- Coordinating shared equipment across multiple job sites
- Ensuring machinery is available exactly when needed to prevent workflow disruptions
4. Budget and Time Allocation
Every resource decision directly affects the project’s financial health and timelines. Strong resource management contributes to:
- Aligning budget forecasts with actual resource usage; a key principle of what is management accounting, where financial insights guide operational decisions
- Identifying cost overruns early and reallocating budgets accordingly
- Avoiding project delays through proactive time planning and milestone tracking
At its core, construction resource management is about achieving balance, ensuring every resource is used efficiently and effectively to drive project success. When done right, it reduces delays, minimises waste, boosts productivity, and keeps the entire project aligned with its goals.
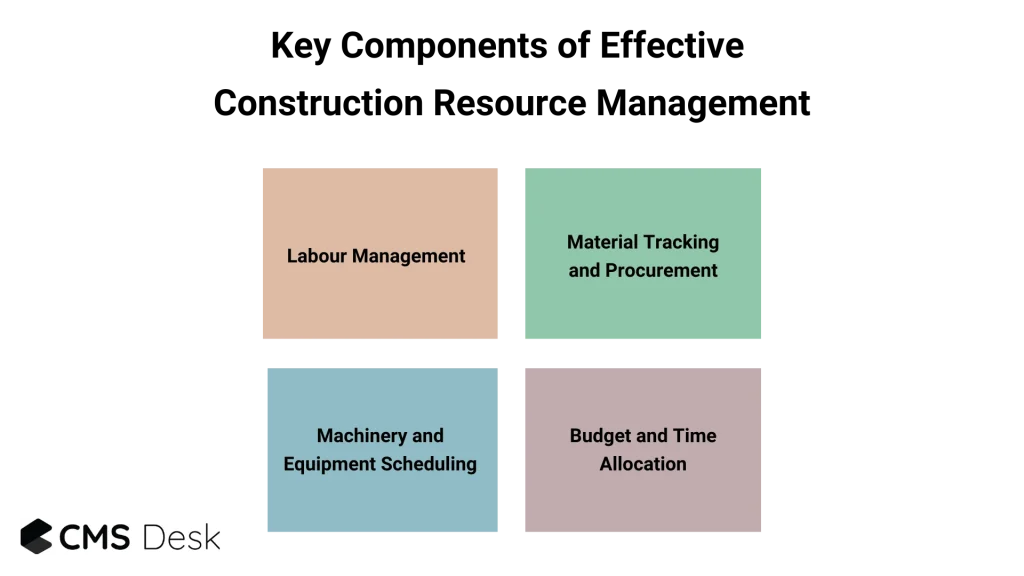
The Benefits of Effective Construction Resource Management
When construction resources are managed well, the benefits go far beyond smoother daily operations. From labour tracking to crew coordination, workforce management software makes it easier to assign tasks, optimise shifts, and reduce downtime across multiple job sites. It’s not just about keeping things organised; It’s about creating a more agile, cost-effective, and performance-driven site environment.
Here are some of the key advantages:
1. On-Time Project Delivery
Construction delays often stem from one simple issue: resources not being where they need to be, when they’re needed. Effective resource management ensures that labour, materials, and equipment are all aligned with the project schedule. This eliminates downtime caused by missing stock, unavailable workers, or unscheduled machinery, helping teams stick to deadlines and avoid costly overruns.
2. Lower Operational Costs
When resources are tracked and planned properly, unnecessary expenses are significantly reduced. There’s less reliance on costly overtime, fewer delays that result in penalty fees, and better control over material usage and equipment wear. By preventing waste and increasing accountability, resource management helps keep projects financially lean without compromising on quality.
3. Higher Workforce Efficiency
With proper allocation of roles, shifts, and tasks, teams can perform at their best without feeling overwhelmed. Workers aren’t left waiting around for tools or instructions, nor are they pushed into burnout from mismanaged schedules. It’s about creating a steady, productive rhythm on-site that maximises output while maintaining morale and safety.
4. Improved Quality Control
Not all tasks require the same level of expertise or equipment. When resources are carefully matched to project needs, you can ensure that the right people and tools are assigned to the right jobs. This targeted allocation plays a key role in maintaining workmanship standards and avoiding quality issues that could lead to rework or client dissatisfaction.
5. Better Data-Driven Planning
Strong resource management generates valuable data, from productivity metrics to usage trends. Over time, this insight can be used to improve cost estimates, project bids, and planning decisions. Rather than relying on guesswork, construction firms can lean on historical data to forecast needs more accurately and reduce risk in future projects.
6. Stronger Collaboration Across Teams
When everyone has visibility into who’s doing what and when, communication improves across the board. Project managers, site supervisors, and office staff can coordinate more seamlessly, reducing misunderstandings or duplication of effort. A shared view of tasks, timelines, and resources ensures all teams are aligned and working toward the same goals.
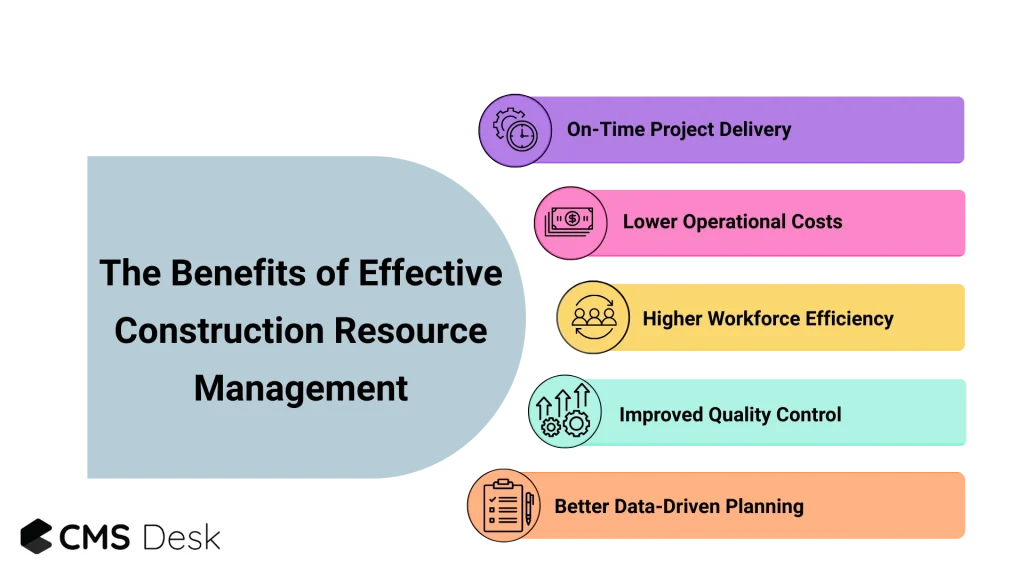
The Real-World Challenges of Resource Management in Construction
No matter how experienced a construction manager may be, resource management is never without its hurdles. From fragmented systems to unexpected delays, keeping track of everything on a busy job site can quickly become overwhelming. And when resource planning falls short, the consequences can ripple across the entire project, causing missed deadlines, budget overruns, and frustrated teams.
Here are some of the most common and pressing challenges faced by construction teams when managing resources on the ground:
1. Disconnected Tools and Manual Tracking
Many construction teams still rely on spreadsheets, whiteboards, or standalone tools that don’t communicate with each other. This leads to duplicated work, outdated information, and missed updates. When systems aren’t integrated, tracking labour, materials, or equipment becomes time-consuming and error-prone, making it difficult to make timely, informed decisions.
2. Poor Communication Between Field and Office Teams
Miscommunication between site crews and back-office staff is a common and costly problem. Whether it’s delayed updates on task progress, unclear shift changes, or inconsistent reporting, poor communication results in confusion, rework, and downtime. Without a shared platform or clear process, critical information often slips through the cracks.
3. Labour and Skill Shortages
Finding the right people with the right skills at the right time is becoming increasingly difficult. Labour shortages, especially skilled trades, can delay key tasks and impact the quality of work. Even when workers are available, mismatches between skill sets and project requirements can lower productivity and increase the risk of errors.
4. Inaccurate Stock and Material Levels
Knowing how much material is available, and where it is, can be a challenge, especially across multiple sites. Without accurate inventory tracking, teams may face material shortages, duplicate orders, or overstocking that ties up budget. Mismanaged stock not only causes project delays but also leads to unnecessary costs and waste.
5. Downtime from Delivery Delays or Equipment Failure
Construction timelines are tightly interwoven, and a single delay can throw the entire schedule off. Late deliveries of materials or unplanned equipment breakdowns lead to idle crews, rescheduled tasks, and increased pressure on remaining timelines. Often, these issues arise from a lack of real-time visibility and proactive planning.
6. Budget Mismanagement Due to Limited Visibility
When there’s no clear picture of how resources are being used, keeping budgets under control becomes difficult. Manual cost tracking, unexpected overtime, or unaccounted material use can quietly eat away at the project margin. Without real-time cost data, construction managers are often reacting to problems after the damage is done.
Recognising these challenges is the first step toward solving them. With the right strategies and systems in place, construction firms can overcome these bottlenecks and create a more responsive, efficient, and resilient approach to resource management.
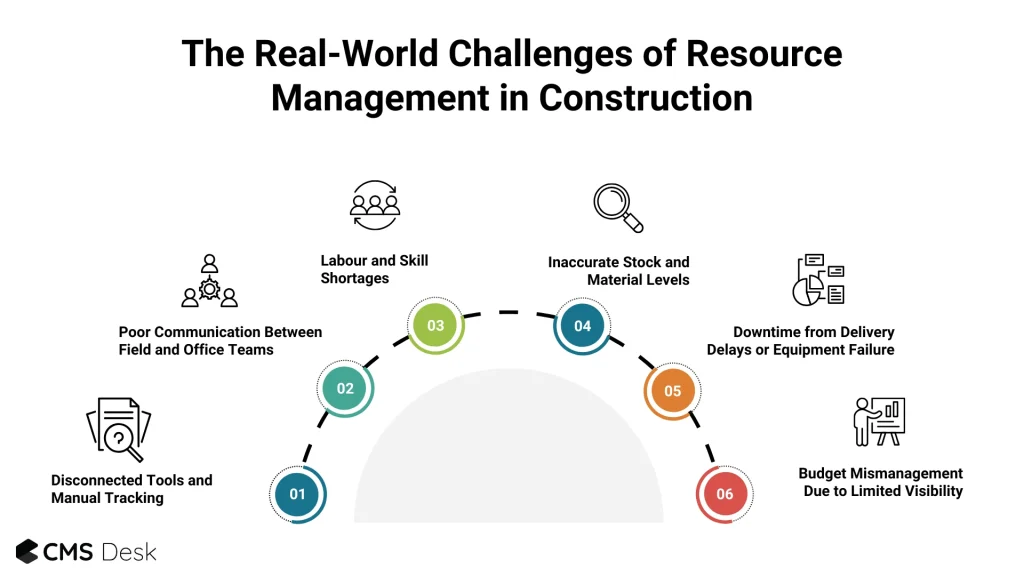
Pro Tips to Master Construction Resource Management
Successfully managing construction resources means combining careful planning with smart technology and clear communication. One of the most effective strategies is to centralise scheduling. Bringing workforce shifts, task assignments, and approvals into a single, accessible platform helps avoid confusion and allows managers to make quick changes as the project evolves. This centralisation ensures everyone knows what they should be doing and when, reducing downtime and miscommunication.
Tracking site activity in real time is another powerful way to maintain control. Knowing who is on-site, their hours worked, and task completion status helps supervisors monitor productivity and costs closely. This is especially valuable in remote or disconnected locations where manual tracking can lead to errors or missed updates.
Digitising stock and inventory management can significantly reduce delays caused by missing or over-ordered materials. By having real-time visibility into what’s available and where, teams can better plan deliveries and avoid costly wait times.
Automating procurement workflows removes the bottlenecks caused by paperwork and manual approvals. Automated processes speed up supplier communication, purchase order tracking, and delivery validation, keeping the project moving smoothly.
Resource planning isn’t just about tools and timelines; It also involves the people behind the work. Strong HR in construction companies plays a crucial role in managing compliance, scheduling, and worker readiness on-site.
Lastly, close monitoring of vehicles and machinery ensures safety, efficiency, and accountability. Proper fleet management prevents unexpected breakdowns and helps schedule timely maintenance.
Together, these strategies create a more efficient, agile construction operation with fewer delays and lower costs.
What Is Automated Resource Management in Construction?
Automated resource management applies intelligent software and integrated digital tools to streamline the planning, monitoring, and optimisation of labour, materials, and equipment. This shift away from manual processes improves accuracy and responsiveness on construction projects.
AI-driven scheduling systems automatically allocate tasks and shifts based on project needs, availability, and skillsets, while sending alerts for any conflicts or changes. This reduces human error and frees up management to focus on strategic decisions.
Live material tracking and logistics coordination provide instant updates on inventory levels and shipment status. This helps teams anticipate shortages or delays and react proactively rather than scrambling at the last minute.
GPS-based fleet and equipment monitoring allows managers to see the location and usage of vehicles and machinery in real time, improving security and ensuring efficient utilisation. It also aids in planning maintenance and reducing unexpected breakdowns.
Automated procurement solutions handle supplier communications digitally, from requesting quotes to tracking purchase orders and confirming deliveries. This speeds up the approval process and cuts down on paperwork.
Centralised HR and compliance platforms keep all personnel data, certifications, and regulatory documentation in one place. This makes it easier to maintain compliance, onboard new workers quickly, and redeploy staff as project demands change.
By integrating these digital solutions, construction teams gain better control over resources, reduce delays, cut costs, and have real-time data to make faster, more informed decisions that drive project success.
Final Thoughts: Build Smarter, Not Harder
Efficient resource use is one of the core pillars of construction project management, directly influencing scheduling accuracy, cost control, and project delivery. When your teams, tools, and materials are coordinated with precision, everything runs smoother.
Digital construction software solutions like CMS Skedge, Stockit, Procure, Onsite, Base, and Fleet give you the control, visibility, and flexibility needed to optimise your resources across every job site.
If you’re ready to manage construction resources more effectively, automation and integration aren’t optional- they’re essential.
Frequently Asked Questions (FAQ)
1. How do I know if my construction project has a resource planning issue?
If you're consistently running into delays, idle workers or machines, last-minute material orders, or budget overshoots, chances are your resource planning needs improvement. Lack of real-time visibility is often a major red flag.
2. Who is responsible for resource management on a construction site?
Typically, project managers and site supervisors handle day-to-day resource planning. However, in well-structured projects, HR teams, procurement officers, and logistics coordinators all play a key role, often supported by digital tools for alignment.
3. Can spreadsheets be enough for managing resources?
While spreadsheets may work for very small projects, they become error-prone, time-consuming, and hard to track across multiple teams and job sites. For growing firms, transitioning to construction-specific software is essential for scalability and accuracy.
4. What is the difference between resource scheduling and resource allocation?
- Resource allocation is about assigning the right people, tools, and materials to the job.
- Scheduling ensures these resources are used at the right time, in the right sequence, without overlap or delays.
Using tools like CMS Skedge helps you manage both in sync, avoiding overbooking or idle time.
5. How do construction teams stay updated on resource availability across sites?
By using integrated apps like CMS Stockit for inventory visibility and CMS Onsite for live labour data. These tools centralise information, so teams across locations can check what’s available, request resources, and avoid duplication or shortage.
6. Is it possible to track resource usage in real-time?
Yes. Platforms like CMS Onsite, Fleet, and Skedge allow real-time monitoring of workforce activity, vehicle usage, and equipment performance. This data is critical for making fast, informed decisions when things change on site.
7. How can I improve communication between my procurement and site teams?
Using systems like CMS Procure and Stockit, you can automate purchase approvals, sync deliveries, and notify teams instantly about material status, minimising miscommunication and wait times.
8. What’s the best way to prepare for unexpected delays in resource delivery?
Use historical data and forecasting tools to plan, but also build flexibility into your schedules. Live tracking apps and smart scheduling software let you quickly reallocate resources to avoid total downtime.
9. How can resource management help reduce waste on construction sites?
Efficient tracking of stock, smart allocation of materials, and better workforce planning mean fewer expired items, reduced rework, and more sustainable use of resources.
10. Can construction resource management impact safety?
Definitely. Overworked teams, missing equipment, or delayed deliveries can all lead to rushed work and safety oversights. With real-time resource visibility, managers can plan safer workflows and ensure the right equipment is always on hand.
Any questions? Get in Touch
1 comment on "How to Manage Construction Resources Like a Pro"
izmir son dakika
-I truly appreciate your technique of writing a blog. I added it to my bookmark site list and will